mathematical models for sheet metal forming processes free download This paper gives an overview on the common classification and characterization of modelling and models in metal forming, as well as introduces a model selection procedure. . A Spider Box is a portable power distribution box that is designed to be an .
0 · sheet metal forming tools
1 · sheet metal forming
Yes, Bosch dishwashers require a junction box installation. The National Electrical Code (NEC) mandates that all electrical connections for appliances, including dishwashers, .
The forming processes of complex panels by computer codes, in addition to extensive practical examples, are recreated throughout the many chapters of this book in order to benefit .
The accuracy of the finite element simulation of sheet metal forming processes is mainly influenced by the shape of the yield surface used in the mechanical model and, in particular, by the number of input values used in the identification of . This paper gives an overview on the common classification and characterization of modelling and models in metal forming, as well as introduces a model selection procedure. .Numerical simulation of metal forming processes, as a component of the virtual manufacturing process, has a very important contribution to the reduction of the lead time. The finite element . The numerical simulation of sheet metal forming processes needs the accurate identification of the material parameters, for a given constitutive model.
design of forming processes is still largely based on experimental techniques, such as the use of circular grid systems (Keeler 1968) or forming limit diagrams (Hecker 1973, Keeler 1974). The .
This paper proposes an inverse isogeometric analysis to estimate the blank and predict the strain distribution in sheet metal forming processes. In this study, the same NURBS .Sheet Metal Forming Processes. Constitutive Modelling and Numerical Simulation. Book. © 2010. Download book PDF. Download book EPUB. Overview. Authors: Dorel Banabic. Necessary to understand metal forming .
junction box wall plate
sheet metal forming tools
In this paper, linear prismatic and hexahedral solid−shell (SHB) elements, along with their quadratic counterparts, have been combined with various advanced anisotropic plasticity .proved by the numerical simulation of various sheet metal forming processes: bulge and stretch forming, deep-drawing and forming of the complex parts. A section has been devoted to the robust design of sheet metal forming processes. Springback is the major quality concern in the stamping field. Consequently, two sections of thisDownload Free PDF. Modelling, Simulation and Control of Incremental Sheet Metal Forming Process using CNC Machine Tool . This paper presents and discusses a mathematical model for capacity management based on different costing models (ABC and TDABC). A generic model has been developed and it was used to analyze idle capacity and to design . A thermal model was built to account for the effects of geometrical parameters of sheet specimen, process parameters and material parameters on the temperature increase of the sheet specimen in .
Sheet Metal Forming Processes Dorel Banabic Sheet Metal Forming Processes Constitutive Modelling and Numerical Simulation 123 Prof. Dr. Ing. Dorel Banabic Technical University of Cluj-Napoca Research Centre on Sheet Metal Forming – CERTETA 27 Memorandumului 400114 Cluj Napoca Romania [email protected] ISBN 978-3-540-88112-4 e-ISBN 978-3-540-88113-1 DOI .CONCLUSIONS The spring back results obtained as a result of the formation of AISI sheet metals having different thicknesses by using air V bending technique with different punch tip radii are as follows: It was determined that as the sheet metal thickness increased, spring back amount decreased. As punch tip radius increased, the amount of .
Functioning as an introducing to modern mechanics principle and other applications that deal with the scientists, mathematics and technical aspects of sheet heavy forming, Mechanics Sculpt of Sheet Metal Molding details theoretically sound formulae . Metal forming processes are used to shape metals into useful products. Rolling is the most common forming process and accounts for around 90% of metal forming. It involves passing metal between rolls to reduce thickness or change cross-section. Forging uses dies and compression to shape hot or cold metal.
The current model accurately predicts the shear cutting process and shows a strong correlation with experimental tests. Two values of clearance (c1 = 0.2 mm) and (c2 = 1.2 mm) are assumed for . The scheme of the hybrid forming process is shown in Fig. 1. First, a thin sheet metal is fixed by a clamping system. The Fixed metal sheet moves downward and is stretched by the die, which is positioned below. After stretch forming, the stretched sheet metal is deformed locally by the tool, which is moved along by NC tool path data.
Sheet Metal Forming Processes Dorel Banabic Sheet Metal Forming Processes Constitutive Modelling and Numerical Simulation 123 Prof. Dr. Ing. Dorel Banabic Technical University of Cluj-Napoca Research Centre on Sheet Metal Forming – CERTETA 27 Memorandumului 400114 Cluj Napoca Romania [email protected] ISBN 978-3-540-88112-4 e-ISBN 978-3-540-88113-1 DOI . Cold roll forming (CRF) is an important sheet metal forming process that is widely studied through experiments and numerical simulations. Mathematical analysis is a more efficient and economical . Keum et al. [8] proposed expert drawbead model which provides the drawing characteristics of the drawbead used in the finite-element analysis of sheet metal forming process to overcome the .
The structure of this paper is as follows: Chapter 2 presents the basics about models and modelling classification. Chapter 3 introduces a model selection procedure for metal forming processes. Chapter 4 presents a selection of important process limits in metal forming regarding the general definition of acting mechanisms and important basics. The presented .On the Pure Mathematical Aspects in Mathematical Models of some Metal Forming Processes . Download Free PDF. . On the Pure Mathematical Aspects in Mathematical Models of some Metal Forming Processes. Tomas Perna. 2012, Mathematical Theory and Modeling. ANNs models are useful in cases that processes' mathematical models are not accurate enough, are not well defined or are missing e.g. in cases of complex product shapes, new material alloys, new .download. Download Free PDF. . A mathematical model was obtained by analyzing the relationship between bending parameters and test results. download Download free PDF View PDF chevron_right. Finite Element Analysis of sheet metal bending process to predict the springback. . -In the sheet metal forming process, in this case V-Bending process .
To utilise established models combined with process data, the following obstacles have to be addressed: (1) acquired process data is biased by sensor artifacts and often lacks data quality . Other studies control the process parameters of incremental forming. Park et al. [14] used the process parameters of the tool size, lubrication condition, and feed rate and then studied the effects of each parameter on the formability. Cerro et al. [15] studied various experimental variables such as tool's feed rate, tool's force, and forming strategy to improve formability.Finite Element Simulation of Sheet Metal Forming Processes using Non-Quadratic Anisotropic Plasticity Models and Solid—Shell Finite Elements . Download Free PDF. . The present work clearly shows that the proposed SHB elements are able to successfully model complex forming process with advanced constitutive equations, using only a single .
The numerical simulation of sheet metal forming processes depends on the accuracy of the constitutive model used to represent the mechanical behaviour of the materials. The formulation of these constitutive models, as well as their calibration process, has been an ongoing subject of research. . Download: Download high-res image (81KB . Forces on a cross-section parallel to the X-Y plane respectively. The values of stress ratio and strain ratio are α = 1/2, í µí»½í µí»½ = 0 under plane strain and plane stress condition. 1.. IntroductionBending of sheet metal is one of the widely used industrial processes, especially in the automobile and aircraft industries. Most sheet metals undergo a combination of bending, stretching, unbending and reverse bending during the forming process [1].Accurate estimation of spring-back in these industries is important [2], [3].Demands in bend .
Analytical models involving first-order [253] and second-order yield criteria [109, 261], slab method [221], upper bound method [15] up to late 1960s have been widely used to estimate forming forces to assist process design.Finite element methods (FEM) have evolved rapidly over half a century since then and nowadays enable the simulation of almost all kinds .Download Free PDF. Sheet Metal Forming Processes: Constitutive Modelling and Numerical Simulation . represents a challenge of these days. The aim of this paper is to achieve a complex analysis on two necking models: Marciniak-Kuczinsky and enhanced Modified Maximum Force Criterion (MMFC) theories. . The accuracy of the finite element . In sheet metal forming, the interaction between virtual models and the real world remains challenging. Process simulations can exhibit significant errors, and reliable measurements are often scarce during early production stages. This study presents a hybrid twin framework that systematically unifies computer-aided design, simulation, and measurement . Finite Element Simulation of Sheet Metal Forming Processes using Non-Quadratic Anisotropic Plasticity Models and Solid-Shell Finite Elements April 2020 Procedia Manufacturing 47(2020):1416-1423
junction box with 3/4 knockout
H. Sunaga, K. Yoneda, A. Makinouchi, Finite element modeling of drawbead in sheet metal forming, in: Proceedings of the Numerical Simulations of 3D Sheet Metal Forming Processes (NU-MISHEET'96 .
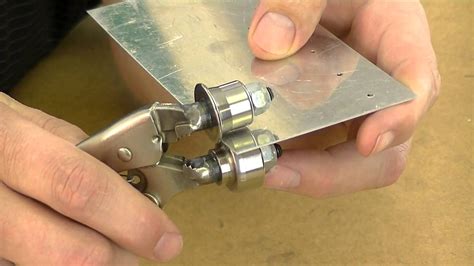
sheet metal forming
junction box wiring guidelines multiple branch circuits
At its core, a CNC woodworking machine is a computer-controlled device that uses specialized software to precisely cut, shape, and carve wood materials. Unlike traditional woodworking tools that require manual manipulation, a CNC machine operates through programmed instructions, allowing for unmatched precision, repeatability, and efficiency.
mathematical models for sheet metal forming processes free download|sheet metal forming tools